Vietnam will host a round in 2020 and is creating a street circuit in Hanoi for the race which will be held at the beginning of April
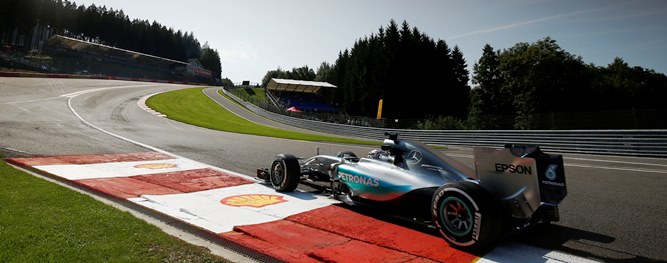
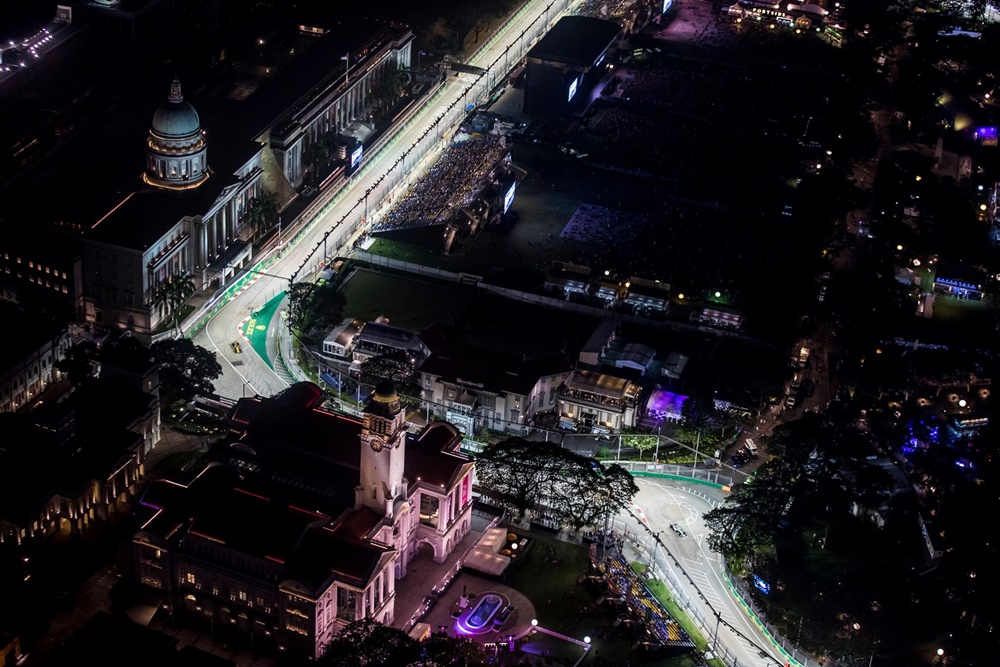
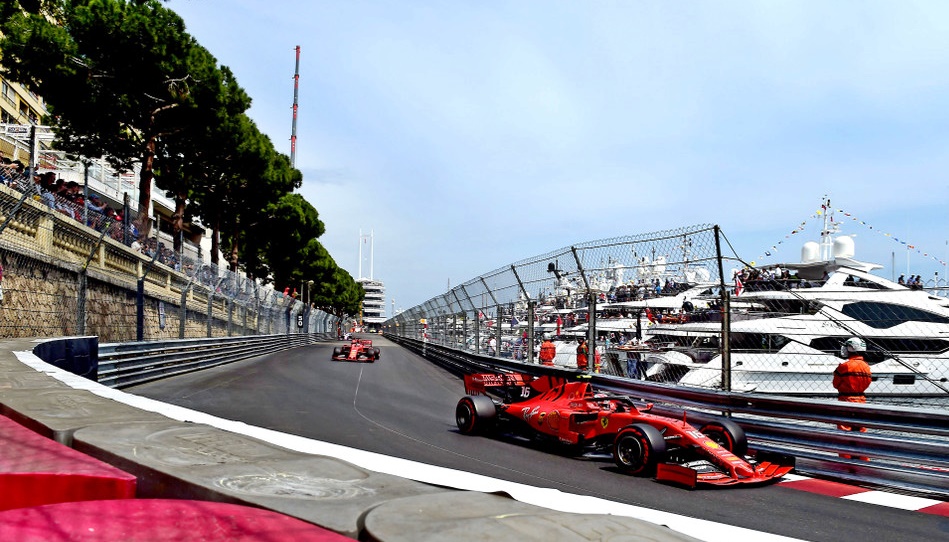
Vietnam will host a round in 2020 and is creating a street circuit in Hanoi for the race which will be held at the beginning of April
Team Proton R3’s third consecutive win in the recent Sepang 1000km (S1K) race certainly grabbed headlines but also deserving praise was the was the impressive result for the team’s third car. This was a Saga with an all-ladies crew comprising Faye Kusairi, Nurul Husna and Leona Chin.
Unlike the other R3 drivers, Faye and Nurul did not have prior experience of competing in the Malaysia Championship Series (MCS). They were selected via the team’s lady drivers search initiative. Leona, however, is a professional racer who has been competing in the MCS.
From 26th to 7th
In the tough 9-hour race, the trio put in a fine effort after starting from 26th position to finish a respectable seventh. A demonstration of team spirit and skill, the 2019 S1K was in fact the first time all three shared the same car.
Despite their unfamiliarity with each other, the inherent speed of all three was evident during practice sessions for the race. They were consistently setting times that put them in the top eight. Their qualifying session however was compromised by a small technical issue, consigning them to start from the back of the M-Production class grid. Nevertheless starting 26th did not dampen their spirit and during the race, they drove with great skill and patience, methodically working their way up through the field.
“The S1K was extremely memorable and surreal for me. I am amazed we finished seventh from 26th on the grid but it proves how quick the Proton Saga and our trio of drivers really is. To be honest, I really feel that if we were given another chance, I think we can make it up on to the podium,” said Faye.
“Our lady race drivers performed admirably and drove really well to mount a great comeback from their low grid position. To finish seventh in what is one of the toughest S1K races in recent memory is a great achievement and the best finish ever achieved at the race for an all-ladies driving crew,” said a delighted Gary Lee, Head of Team Proton R3.
Proton Saga proves racing prowess
Despite being R3’s newest car, the 2019 Proton Saga has already proven its ability to be a quick track car. The short development cycle (the model was launched in August this year) meant the team faced a tremendous challenge to get it ready on time, but the results have proven how suitable the Saga is for motorsports.
“The Proton Saga is a model synonymous with Proton and was the very first model the company used for motorsports. In more recent times, we favoured other models but last year we started using it again for the MCS and S1K in 2018. This year’s car is brand new and despite the very short timelines, the results have been very impressive. This therefore proves the Proton Saga is capable of performing in a variety of environments, from daily commuting to family outings and competing in Malaysia’s biggest race, making it truly a Malaysian favourite,” said Dr Li Chunrong, CEO Of Proton.
Proton R3 wins Sepang 1000km again – that’s 3 years in a row!
For nearly as long as there have been cars, people have been collecting and customizing them. Until recently, however, if owners of classic cars wanted to replace a damaged bonnet or fender on an out-of-production model, they had to search through junkyards or hire a craftsman to make a one-off replacement (which might be costly).
Now, thanks to a new technology called dual-sided die-less forming, Nissan plans to offer original specification pieces at mass-production prices. Automakers traditionally form body parts by pressing sheet metal against specially created dies. Designing and building multiple dies for each part is expensive and only pays off after stamping a large volume of parts. This is why, for locally-assembled models, many body parts are imported from a bigger plant elsewhere as the volume locally is too small to justify the investment in huge stamping machines.
This basic process has remained largely unchanged since the early days of mass production of motor vehicles. It remains a stumbling block that prevents production of low-volume parts unless costs are raised.
Nissan’s new dual-sided die-less forming technology presents a compelling alternative to the investment-intensive industry norm. It does away with dies and stamping machines altogether, removing one of the most costly and time-consuming steps in auto body manufacturing.
Two robots better than one
The process involves two robots working on opposite sides of a flat sheet of metal. By syncing their movements precisely and using diamond-tipped tools developed by Nissan, the robots can shape the metal to a high degree of accuracy and detail. Working in tandem, two robots can produce intricate concave and convex shapes that could not be created if one robot were working from a single side of the sheet.
The new technique was made possible, thanks to the production engineering expertise at Nissan’s Production Engineering Research and Development Centre, along with advancements in materials technology by Nissan’s Research Division.
“About five years ago, we started thinking about ways of forming sheet metal without relying on dies,” said Keigo Oyamada, an assistant manager in Nissan’s vehicle manufacturing element engineering department, who oversaw the project. “Our goal was to solve the cost issues related to creating dies for small-volume production. We want to put this technology to use to create spare parts for old models whose dies have already been thrown away, or potentially even to let people order custom parts from Nissan.”
Performing a 3D scan of an existing part creates data that can be used to ‘teach’ the robots to build the scanned part — although some human guidance is still required. This approach will allow Nissan to produce parts that haven’t been made in decades, simply by scanning existing examples of those parts.
Custom parts – in just one week
Dual-sided die-less forming can be used to create custom body parts in less than a week, instead of waiting as long as a year for dies to be designed and manufactured. The process is also inherently adaptable; it can be used to produce small and large parts alike, as well as car parts other than body panels.
For now, Nissan plans to use dual-sided die-less forming to produce replacement parts for cars the company no longer sells. Looking further ahead, the company sees potential for creating customized parts for those who are looking to add a little uniqueness to their future rides.
For assistance in obtaining Nissan Genuine Parts in Malaysia, visit www.tceas.com.my.
James Bond, undeniably the world’s best-known secret agent, has driven a great variety of cars in the past 57 years since he first appeared in Dr. No. Many were sportscars and thanks to Q branch, some of them had fancy accessories like rocket launchers, ejection seats, machine guns and tyre-shredders. Being an agent of the British government, Bond often drove the latest British models with Aston Martins featuring prominently in the last few adventures.
In April 2020, No Time To Die, the 25th official James Bond film (and the fifth one starring Daniel Craig as Agent 007), will premiere and as with the previous films, there will be exciting car action. Seeming to reflect trends in the market, there will be more SUVs and in fact, the New Defender from Land Rover will appear prominently on the big screen. This will be the first movie to feature the New Defender which was launched in September this year.
Other Land Rover models you will see at different points in the movie will be the Range Rover Sport SVR, Land Rover Series III and Range Rover Classic. The British 4×4 manufacturer has had a long-standing partnership with EON Productions on the Bond films which goes back to 1983 when a Range Rover Convertible appeared in Octopussy.
Land Rover’s design team worked closely with Special Effects and Action Vehicles Supervisor Chris Corbould on the specification of the Defenders in the film. Based on the Defender X model in Santorini Black, with darkened skidpans, 20-inch dark finish wheels and professional off-road tyres, they were the first Defenders to be built at Jaguar Land Rover’s new production facility in Slovakia.
Stunt coordinator Lee Morrison (shown below) and stunt driver Jess Hawkins pushed the vehicle to extremes, making maximum use of pioneering off-road tech, 900 mm wading ability and 291 mm ground clearance for No Time To Die’s spectacular car chase action.
“Designing and co-ordinating the action sequences for the Bond franchise requires a non-compromising mindset. We needed an unstoppable vehicle to help us battle against the elements, steep descents and river crossings so we chose the new Defender. I’m beyond impressed that the Defender is not only back but much, much better!” said Morrison.
Just as Lexus and Mark Levinson have had a long relationship (almost 20 years) in the area of audio systems, Bentley has collaborated with Naim for the past 10 years, in the development of the most powerful, best-in-class in-car audio systems. The latest ‘Naim for Bentley’ is said to set a global benchmark for interactive sound technology offering occupants concert hall quality sound.
Naim for Bentley delivers the world’s most advanced music systems, both inside the world’s most prestigious road cars and also for listeners at home. Bentley’s new Flying Spur has Naim’s superlative audio system seamlessly integrated into state-of-the-art British craftsmanship.
21 speakers and 2,200-watt amplification
The sound system features 21 speakers with 2,200-watt amplification and Active Bass Transducers. Eight DSP sounds modes are available and the car exhibits illuminated speaker grilles. Sound settings can be accessed via an elegant 12.3-inch HD touchscreen interface at the centre of the dashboard. Customers can configure this in a variety of ways: as a single display, split 2:1 or showing different functions at the same time. The overall designs highlights simplicity of use with a contemporary and elevated aesthetic.
Aiming to break sonic boundaries
Bentley Motors and Naim Audio are now working together to create new products for 2020 which continue to break sonic boundaries. The close confines of a car cabin capable of travelling at speeds of over 320 km/h, combined with engine, road and wind noise, provide a challenge for Naim’s engineers, quite unlike the demands of achieving best replay performance in the home or studio.
To bring true Naim sound quality into this unique space, engineers of the two companies have flatly rejected traditional approaches, in the process rewriting the rulebook of in-car audio systems. The result? New worldwide benchmarks for in-cabin sound technology and incredible depth of music quality that has to be heard to be believed.
Naim is a Queen’s Award winner for its innovation and having recently come out with a trailblazing Digital Signal Processing (DSP) system, it realised it could apply an all-new approach to the in-car implementation. The DSP system would find itself at the very heart of the Naim for Bentley audio system, enabling a degree of tuning previously not possible, ensuring optimal sound performance whatever the speed or road conditions.
Each new generation of Bentley has seen a refinement and an update from the original Naim for Bentley audio system. Beginning as a 15 speaker – 1,100-watt system in 2008, the system has evolved into a 2,200-watt amplifier feeding 21 speakers as featured in the new Flying Spur.
The Naim for Bentley system has been designed to maintain performance even when the roof of the Continental GT Convertible is down, and as Bentley evolves its hybrid car line, beginning with the Bentayga Hybrid, the even quieter engines offer a different audio environment to design for altogether.
Unique Digital Signal Processor solution
Naim has engineered a unique Digital Signal Processor (DSP) solution for the Naim for Bentley audio system. This innovative technology offers a range of modes to optimise the in-car soundstage, depending on seating position and listening preferences. It ensures ultimate audio performance is maintained whatever the speed or road conditions.
While class-leading, with an extremely powerful amplifier, the Naim for Bentley system is more than just a sound system. It has been engineered to deliver a true high-fidelity experience matched to the refinement of the Bentley experience.
Naim for Bentley’s audio system is compatible with Spotify, Apple Music, TIDAL, Deezer and allows customers to enjoy their own choice of music, digital radio or spoken word media such as audio books and podcasts.
Bentley Flying Spur First Edition to be auctioned for Elton John AIDS Foundation
© Copyright – Piston.my 2024 Trademarks belong to their respective owners. All rights reserved