The SF90 Stradale, Ferrari’s hybrid plug-in electric vehicle (PHEV), has been joined by a topless version – the new SF90 Spider. Just as the SF90 Stradale was the brand’s first PHEV, the SF90 spider is its first production PHEV spider.
Though it loses its roof (when desired), the SF90 Spider’s performance is not compromised and it has the same extreme supercar specification. The retractable hard top (RHT) is the latest version of Ferrari’s signature retractable hardtop architecture.
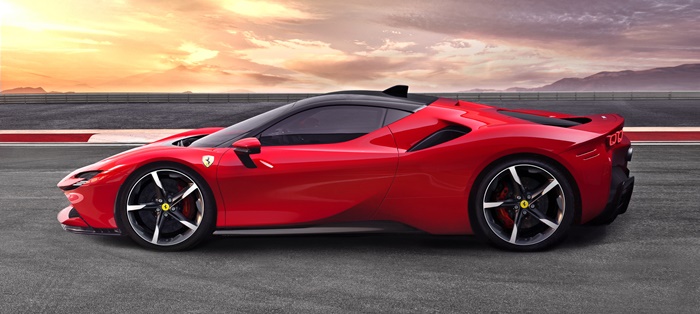
14-second operation
The RHT is so simple that it can open or close within 14 seconds, with operation possible even when the car is on the move. The use of aluminium in its construction also means that it is around 40 kgs lighter than a conventional retractable hardtop. Its compactness requires just 100 litres of space, rather than the 150 – 200 litres required by a traditional system.
Ferrari guarantees optimal noise insulation and protection from the elements when the RHT is raised and it will not deform at high speeds. An adjustable electric rear window also enhances occupant comfort, even when the RHT is lowered at higher speeds.
The hybrid architecture proved a challenge in terms of weight management. While the extra 270 kgs of the hybrid system was amply compensated for by the extra power delivered, extensive optimisation and weight reduction work was also required on the rest of the car to keep overall weight down to 1,670 kgs.
Just as the SF90 Stradale redefined the aerodynamic performance levels of the Ferrari range, the SF90 Spider is pushing the limits of the results delivered still further. The goals that drove the aerodynamic development of the car from the very earliest stages were maintaining the SF90 Stradale’s performance levels with the RHT deployed, minimising aerodynamic turbulence and noise with the RHT retracted, and optimising power flows.
Unmatched downforce and aerodynamic efficiency
The downforce and efficiency figures are said to be unmatched by any other car in the category. The main features in the SF90 Spider’s aero design include the shut-off Gurney at the rear, an active control system that varies downforce over the rear axle, the front underbody with vortex generator strakes, and forged wheels with wing profiles. The results: a massive 390 kgs of downforce generated in cornering at 250 km/h (with the special Assetto Fiorano specification).
In a first for a Ferrari production spider, the SF90 Spider has plug-in hybrid architecture in which the internal combustion engine is integrated with two electric motors at the front and one at the rear derived from and named after the MGUK (Motor Generator Unit, Kinetic) used in Ferrari’s F1 cars.
Most powerful Ferrari production V8
The synergy between the turbocharged V8 petrol engine and the electric motors generates a maximum of 1,000 ps/900 Nm, with 60 ps more than any other V8 turbo engine ever built by Ferrari. The 8-speed, oil-bath, dual-clutch gearbox used in the SF90 Stradale has been redesigned for the spider version.
Much attention was given to sound quality when redesigning the exhaust system as the soundtrack is one of the pivotal factors in the exhilarating pleasure of driving a Ferrari. The introduction of a ‘hot tube system’, which transfers sound more directly to the cockpit, has produced fuller, richer harmonics across the entire frequency range, improving both in-car sound quality and intensity as revs rise compared to previous Ferrari V8s.
To make full use of the powertrain’s output, the engineers improved the vehicle dynamics systems to allow the driver to enjoy the maximum potential, and not just in terms of pure performance and lap times. The new hybrid architecture required extensive integration work on the car’s many different control logics, which led to the development of the new eSSC (electronic Side Slip Control) vehicle dynamics control system.
Digital instrumentation with HUD
The look and feel of the cabin was driven in large part by the complete redesign of the HMI (Human-Machine Interface). The instrumentation is now predominantly digital with all the screens going completely black when the car is not running. The central instrument cluster comprises a single 16-inch HD screen, complemented by a head-up display.
The steering wheel completes that transfer process from the competition world and also ushers in a new era by introducing a series of touch commands that allow the driver to control virtually every aspect of the car without ever taking the hands off the wheel.
The F1 bridge, a signature on the previous models, has now disappeared from the central tunnel and been replaced by a modern take on the gearshift gate, an iconic feature of Ferrari’s manual gearboxes. In the new gate, however, the gearshift grille is digital as befits an automatic transmission.
Going to the limits
As is the case with the SF90 Stradale, the SF90 Spider is also available with an option for owners who want to go right to the edge of the performance envelope. They can specify the Assetto Fiorano pack with upgrades such as Multimatic shock absorbers. Others include the adoption of high-performance materials (such as carbonfibre and titanium), a carbonfibre rear spoiler and road-homologated Michelin Pilot Sport Cup 2 tyres designed to improve track performance in the dry.
The first customers of the SF90 Spider can expect to get their cars during the second quarter of 2021. Each of them will pay prices that start from €473,000 (around RM2.3 million) in Italy.
Ferrari SF90 Stradale PHEV starts new era for The Prancing Horse, priced from RM1.91 million