Six years after it appeared, the BMW i8 Coupe will be retired as its production cycle comes to an end. A success story as a unique symbiosis of futuristic design and pioneering technology, it was the BMW Group’s first plug-in hybrid model that spurred interest and excitement for electrified drive technology and laid the foundation for the BMW Group’s now broad range of plug-in hybrid models.
At the same time, the i8 developed into the world’s most successful sportscar with an electrified drive system. With more than 20 000 units sold since 2014, it achieved higher sales than all competitors in its segment combined. Its global market share has been more than 50% in the segment of sportscars with electrified drive for years and the i8 will be able to maintain this leading position until the middle of April 2020.
The i8 began as the BMW Vision EfficientDynamics, a concept car shown at Frankfurt Motorshow in 2009. The response was very enthusiastic, and BMW said that the central features of its design and technology would be transferred to a production model of the new BMW i brand.
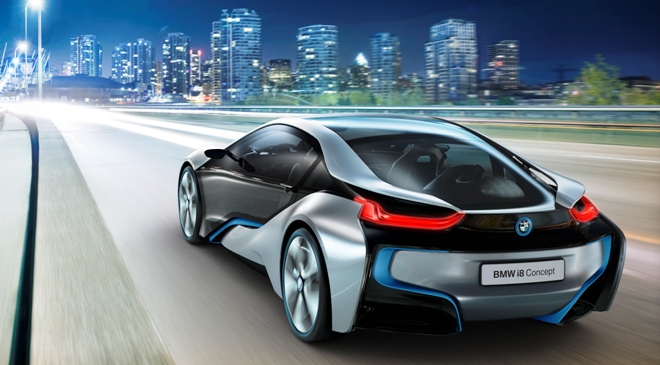
Launchpad for electrification strategy
The i8 had its world premiere at the same motorshow 4 years later, together with the i3. The double debut was the starting signal for implementing a comprehensive electrification strategy, with which the BMW Group set the early and consistent course for a model programme geared towards sustainable driving pleasure.
Today. Pure electric and plug-in hybrid models are available in all relevant segments, from the compact and midsize class, through the BMW X models, to sportscars and luxury sedans. The BMW Group plans to expand its range to include 25 electrified models by 2023, more than half of which will run on electric power alone.
Pioneer and flagship
As a pioneer and flagship for driving pleasure with plug-in hybrid technology, the i8 was an ideal car for the job right from the start. New paths were forged with the BMW i specific vehicle architecture and the plug-in hybrid system. The combination of a passenger cell made of carbonfibre reinforced plastic (CFRP) with an aluminium chassis was just as revolutionary as the intelligently controlled interaction of the combustion engine and electric motor.
The control of its plug-in hybrid system was designed both for dynamic power delivery and for the most efficient interaction of the two engines. The combustion engine with BMW TwinPower Turbo technology transfers its power to the rear wheels. The electric motor drives the front wheels. The result is a hybrid-specific all-wheel drive with a noticeably positive influence on traction, agility and driving stability.
This, and the spontaneous power delivery of the electric motor with a maximum torque of 250 Nm available immediately from standstill, means that the sporting character of the i8 also comes into its own in purely electric and therefore locally emission-free driving. Up to 120 km/h can be reached in pure electric driving mode and the combined drive torque of both powerplants unleashes performance characteristics similar to a high-performance sportscar.
Beyond eDrive technology
Right from the start, the pioneering function of the i8 extended far beyond establishing BMW eDrive technology in an iconic sportscar. The extensive use of CFRP in the body structure and the clearly visible measures to reduce air resistance set new standards in the areas of intelligent lightweight construction and aerodynamics. Together with the i3, the sportscar also paved the way for innovative manufacturing technologies, with which the BMW Group became a pioneer in the use of CFRP in the industrial production of volume-produced automobiles.
Already a milestone in the history of the BMW Group
The Leipzig plant is currently producing the 200 units of the limited Ultimate Sophisto Edition of the i8. One of the edition models was already manufactured in December 2019 as the 20,000th unit of the model. Among the milestones in the history of sportscars, its sales figures are well ahead of classics such as the M1, of which only 399 units were produced for road use, and also ahead of the Z8 roadster, which was built in some 5,000 copies.
Click here for other news and articles about BMW.