53-year-old Gerrit Braun and his twin brother, Frederik, founded Miniatur Wunderland in Germany’s Hamburg Speicherstadt district 20 years ago. It’s an exhibition space which measures more than 10,000 square metres in size and visited by around 1.4 million visitors a year.
If you have the time to count them, there are 9,250 cars, 269,000 figures, 15,715 metres of track, 1,040 trains with more than 10,000 carriages, 4,340 buildings and 130,000 trees. You’ll find cities, villages, mountain panoramas, an airport, artificial northern lights, and even a fair. It took over 300 employees who spent around one million hours to create this miniature world.
The scale of the models is 1:87 and many of them are Porsche sportscars, including the 99X Electric which was added recently. But unlike other miniature worlds, there will be cars that not just move but also race – just like the real thing, only smaller.
Project started in 2015
The motorsport project has been ongoing since 2015 and it’s their biggest challenge to date. It encompasses the redesigned south of France, which will officially open in the first half of 2022, and features the legendary Monaco Grand Prix course.
“We’ll alternate between Formula One and Formula E races,” said Braun. “Everything true to the original, with parade lap, safety car, starting grid – and then action!”. For visitors to have the perfect view of all the racing action, the Miniatur Wunderland team first had to shrink Monaco. Like everything else, the principality on the French Riviera was reproduced at a scale of 1:87. The racing cars are just 6 cm long and their top speed of 85 cm per second would translate to nearly 270 km/h in the real world. This is as realistic as it gets – but that’s also what makes the whole undertaking so difficult.
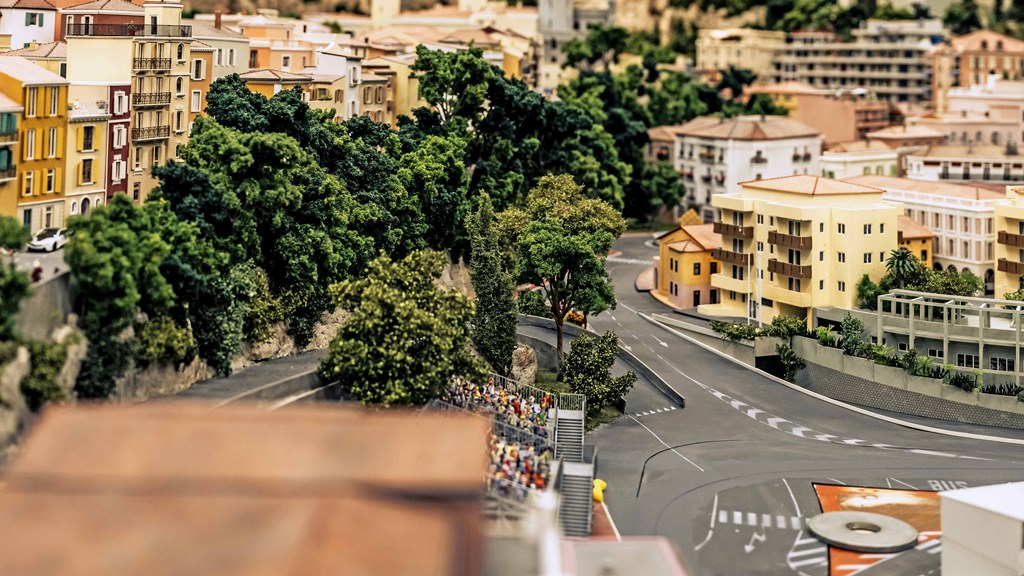
A scenario never built before
A small-scale scenario this realistic has never been built before. Everything had to be created from scratch. The software responsible for controlling 20 racing cars was developed on their own computer. The system responds to the driving manoeuvres of the other racers within 50 milliseconds, so each race is different. With real battles for position, passing manoeuvres, and occasionally even a crash. “Of course, we want to avoid that, if at all possible, because then the Safety Car has to come out and a couple of people are kept busy for some time,” Braun said.
While the race simulations are already running in the computer, Braun still has to teach the cars to accelerate at just the right moment. “The software always wants to maintain the lead, but sometimes you just need to slow down during a race. Programming all that is a complicated process,” he explained.
The small electric cars are powered by magnetic fields. The 21-metre course through miniature Monaco is made up of 24 special circuit boards with a total of 1,400 magnetic field sectors, each of which is controlled separately and generates its own magnetic field.
3D-printed racing cars
While the software still needs some work, the racing cars are ready to race. They were created using the model building experts’ 3D printer and sheets of plastic just 0.03 mm thick. 3D data comes from companies like Porsche Motorsport which provided data for the 99X Electric used in Formula E.
The chassis are painted over multiple times and faithfully reproduced down to the smallest sponsor stickers to reflect their full-size counterparts. The underbody conceals a Halbach array, a diamond-shaped panel that serves as the counterpart to the magnetic fields along the course.
If everything goes according to plan, the miniature car races will be the Hamburg team’s next global milestone in the field of model building. “The crowning achievement of all our efforts,” said Braun. “Even more complex than the airport with its airplanes taking off and landing, which was commissioned in 2011.”
Time cannot be shrunk
The fact that the masterminds of miniaturization have been working on the ambitious idea of a real racecourse for 6 years demonstrates their passion as well as the sophistication of the project. But Braun reveals one unsolvable problem with miniaturization: “We may be able to shrink down objects, but we can’t shrink down time.”
Abdul Wahab’s 1986 Daihatsu Mira van will be Malaysia’s entry in Hot Wheels Legends event