The ASEAN Free Trade Area (AFTA) was conceptualised in the early 1990s and all the member nations signed an agreement to establish it in 1992. It was intended to create a regional trade bloc where goods and services could be exchanged between ASEAN countries with preferential tariffs .
The AFTA agreement’s main feature was the Common Effective Preferential Tariff (CEPT) which required all ASEAN members agree to adopt the same tariff structure and impose import duties of between 0 and 5% on goods and services which originate from any ASEAN country. A condition is that at least 40% of the content of the goods should be of ASEAN origin, besides being made in one of the ASEAN countries. This applies to finished goods, like complete vehicles, as well as components.
The benefit of AFTA to carmakers
Why have AFTA? The simple answer would be strength in unity and size. Having AFTA also means that instead of separate small markets, there will be a single larger one which can be treated as a single common market and estimates in the 1990s already placed the number of consumers at over 550 million – larger than the European Union then. Many ASEAN consumers were already in the middle class or moving into it (although the financial crisis of the late 1990s slowed things down a bit) and this increasing prosperity has certainly very attractive to companies doing business globally.
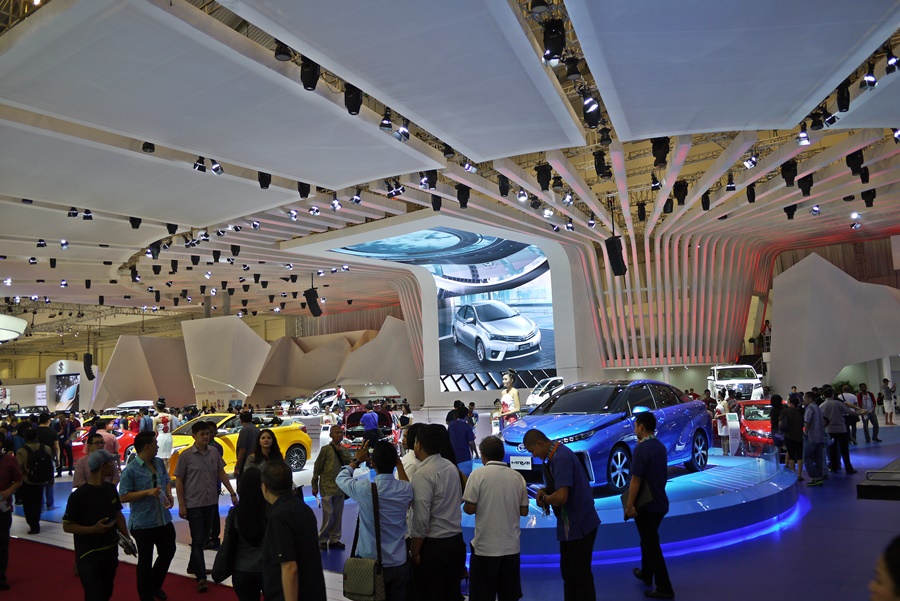
For carmakers, AFTA was an attractive idea and during the 1990s, a number of global players began to establish big factories in Thailand and Indonesia. These would become regional hubs for certain popular models and as there would be no import duty imposed exporting vehicles between ASEAN countries, it was as good as making them in each country. The major advantage was that concentrating production in a single factory meant bigger volumes which would provide the vital economies of scale to push production costs down and have more attractive pricing.
Groupe PSA, the French automobile conglomerate with brands like Peugeot and Citroen in its group, also looked at AFTA but didn’t see the right numbers in the 1990s, and it was also focused on China which was then a fast-growing market. However, they kept an eye on the market growth in ASEAN and in Malaysia, where their partner is Naza Corporation, Peugeot sales were growing rapidly and accounted for 86% of the volume sold in ASEAN.
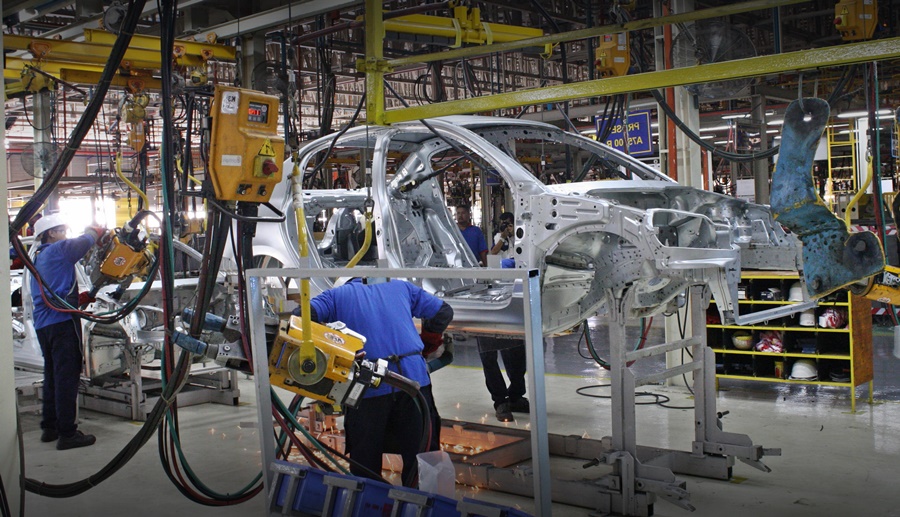
Malaysia’S Naza Automotive Manufacturing plant becomes a regional hub
The Malaysian company also had its own assembly plant in Kedah and with Naza having proven its commitment, Groupe PSA made the decision to use Malaysia as its regional hub. The decision was announced at the Peugeot World Conference in January 2010. However, planning took some time but, in the meantime, Groupe PSA began small volume production of a Peugeot model at Naza Automotive Manufacturing (NAM) as a shared operation.
Early last year, the French company acquired a majority stake in the business operations of NAM which began operations in 2004. Groupe PSA and Naza will jointly produce Groupe PSA-branded cars for Malaysia and other ASEAN markets which now has a potential customer base of 680 million. Further opportunities will also be explored beyond ASEAN, with a potential to contribute significantly to Malaysia’s economy.
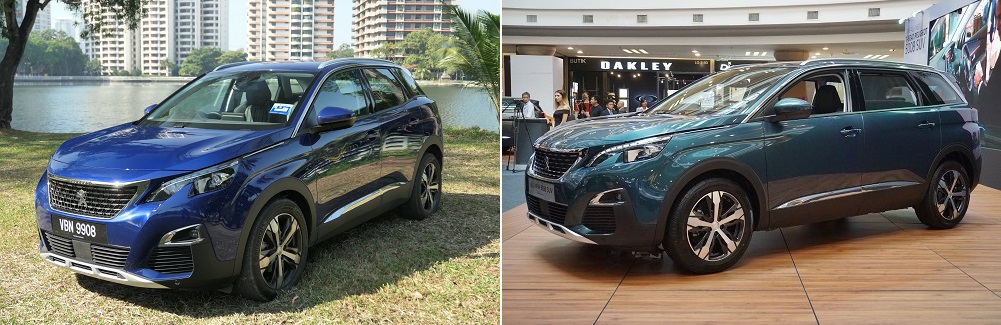
First exports to the Philippines
This month, NAM will begin exporting its first shipment, a batch Peugeot 3008s, to the Philippines. “The Peugeot 3008 with the Peugeot 5008 1.6 THP are targeted to be available in the Philippines with more than 4,000 units by 2023. The Philippines is the first ASEAN country where our cars manufactured at NAM is being exported to under the AFTA,” said Laurence Noel, Head of ASEAN & CEO of Naza Automotive Manufacturing, Groupe PSA. “More cars will be exported to other ASEAN countries very soon,” she added.
Find out more about the Peugeot 3008 and 5008 at www.peugeot.com.my.